The Down and Dirty:
Heavy-Duty Grease
How heavy-duty greases are built tough to increase machine performance and protect against the unrelenting elements and threat of contamination
Heavy-Duty greases have a big job to do. They have to excel at lubricating under extreme conditions so construction, agriculture, transportation, and mining equipment operators can get the most out of their machinery.
So, what are the considerations when creating a grease that can perform better with heavy-duty and high-load carrying equipment? This month’s blog does the heavy lifting on heavy-duty greases, detailing what you need to know to protect your equipment and maximize service life.
What Operating Conditions Affect Heavy Equipment?
While there are many grease technologies engineered to extend machine life and decrease downtime, in the case of high-load carrying and heavy equipment, the operating conditions can cause several lubrication problems that impact performance.
- High Heat
- Force and Vibration
- Contamination
How Do Heavy-Duty Greases Handle These Conditions?
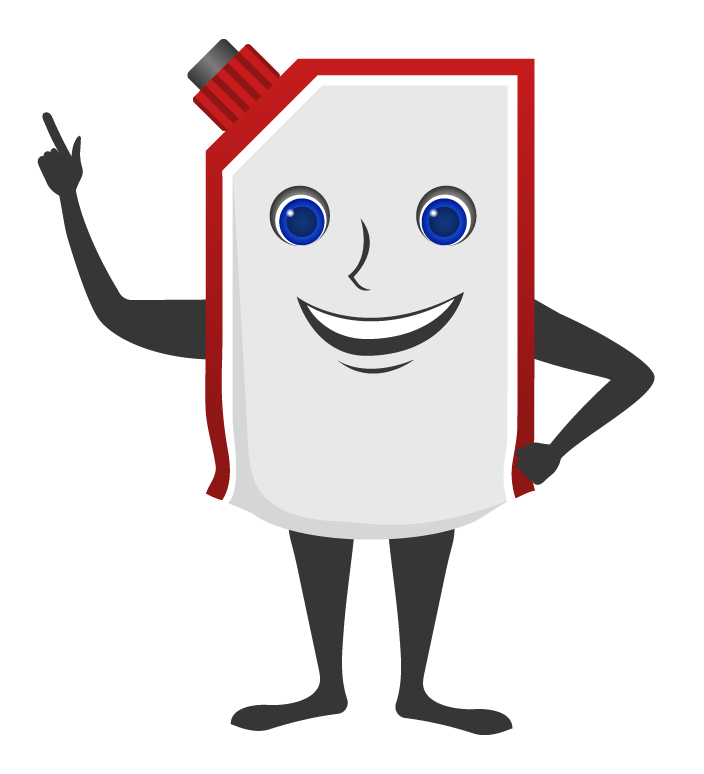
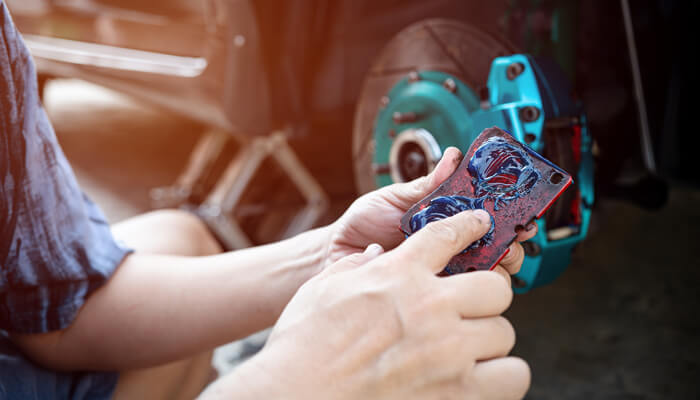
A variety of factors determine the ideal heavy-duty grease for your application. Here are a few examples:
- Water Resistance
All heavy-duty greases need a measure of water resistance to stay put in humid or wet environments and still do their job. Saltwater and freshwater can also cause damage — whether from natural exposure or regular equipment washdowns.
- Wind Resistance
- Temperature Rating
Greases not rated for certain high or low temperatures can melt or freeze, hampering equipment performance. Remember that NLGI categorizes greases by consistency into nine grades of hardness from 000 (fluid) to 6 (very hard). The most common is NLGI #2 because it can be used for a wide temperature range.
- Friction Reduction
- Viscosity
Viscosity determines how thick or consistent the grease is. Did you know the viscosity of grease matters in different seasons? When it’s hot in summer, grease tends to become thinner, so it’s important to use a thicker grease that has a high viscosity and can better stay in place. The opposite is true for cold winter months when it’s better to choose a low viscosity grease that can be pumped and can flow into machinery joints more easily.
- Ease of Application