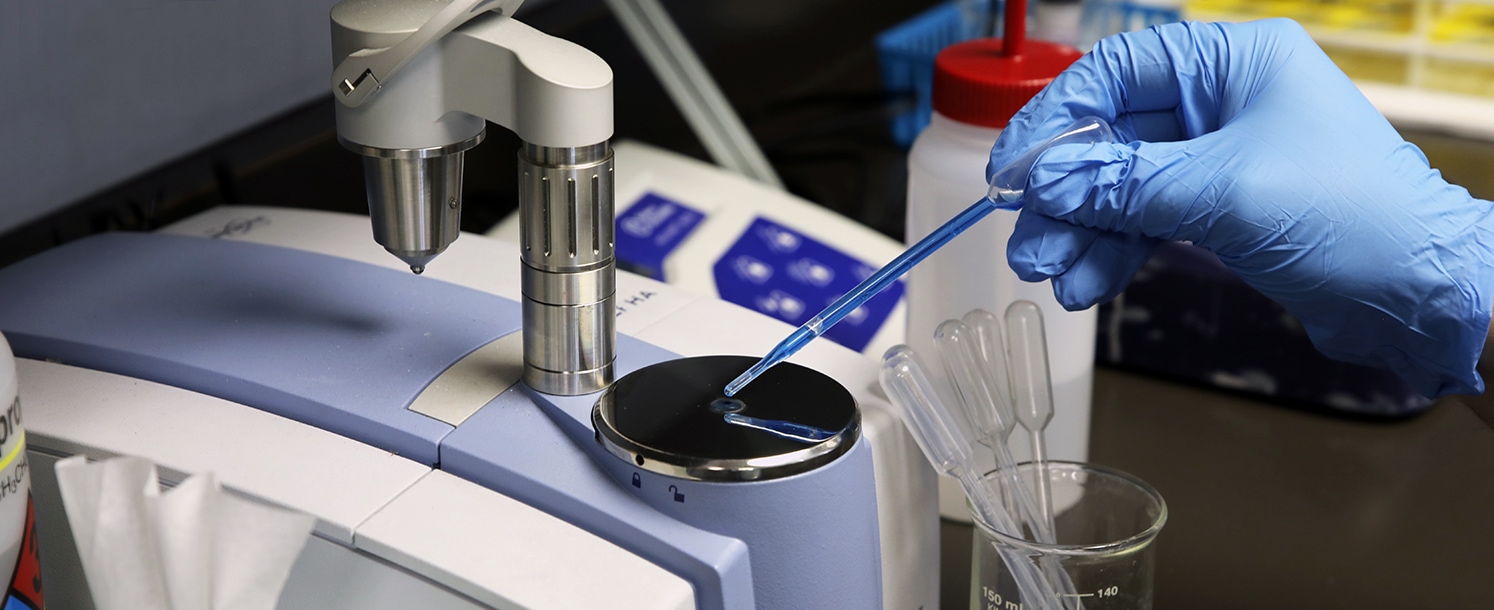
RAISING THE BAR
Our Quality Commitment
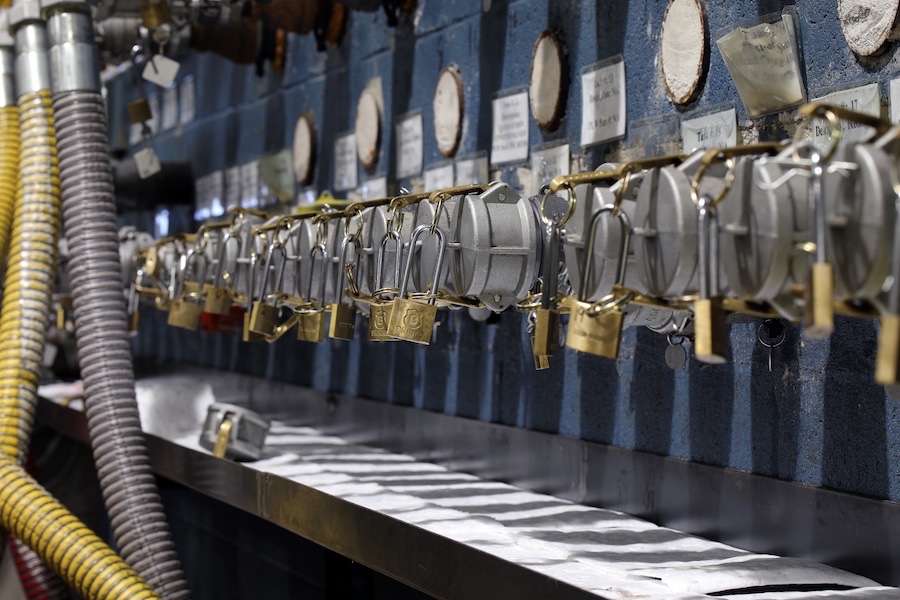
Holding the highest standards
Acceptable Failure Rate
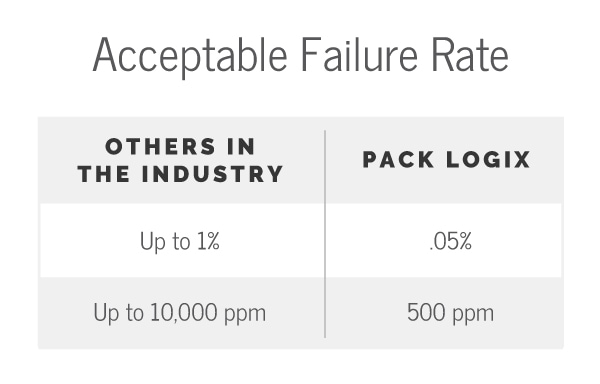
A visual representation
What Does a 0.0005 Failure Rate Look Like?
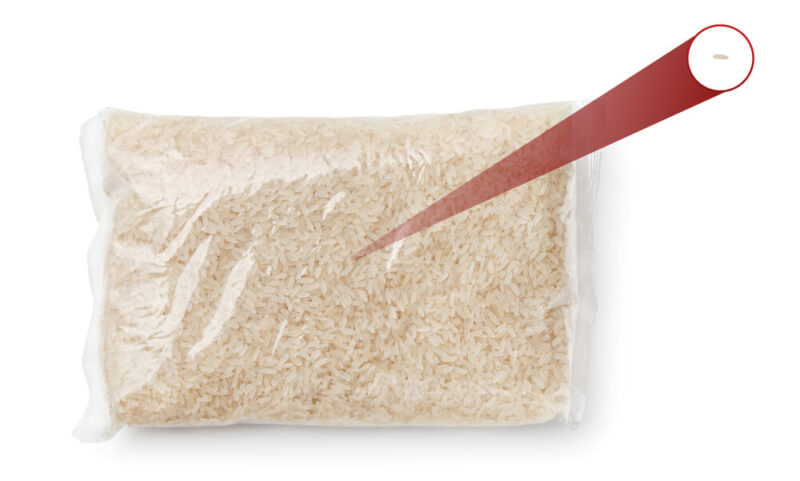
.05% is the equivalent of 1 defective grain of rice per one pound bag
Our Investment in Excellence
The Cost of Quality
At Pack Logix, the cost of quality (COQ) is an investment in excellence and a reflection of our unwavering commitment. While others in our industry focus on end-of-the-line post-production issues, we take a proactive approach, investing upfront in upholding the highest quality standards to avoid the higher costs down the line associated with rework and replacements.
Investing $1 upfront saves $3 in potential rework and replacements.
We recognize that every time rework occurs, it can add significant costs. A pallet of products requiring rework must be segregated, inspected, and manually checked, which introduces human error and increases labor costs. For instance, while a machine might fill 60 bottles a minute at a minimal cost, manual inspection is much slower and more expensive. This labor-intensive process adds considerable expense and complexity, which is why we strive to get it right the first time, every time.
Our proactive approach minimizes the risk of shipping faulty products, ensuring that any defects are identified and corrected before they reach our customers. By maintaining this high standard, we uphold our commitment to delivering superior quality with every fill.
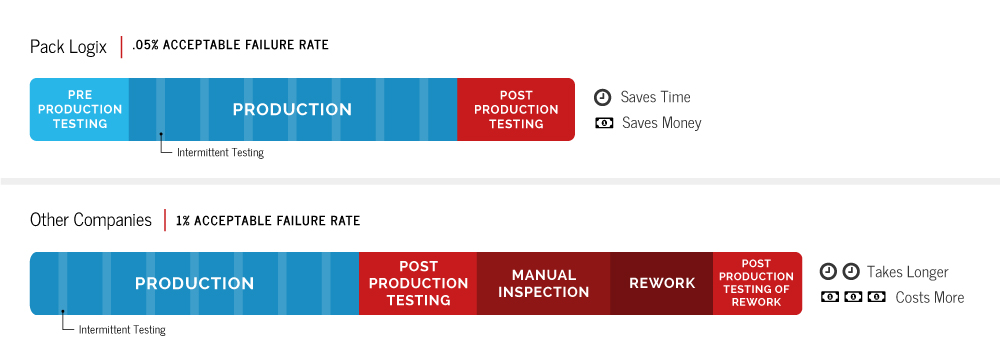
Ongoing Diligence
The Pack Logix Testing Process
At Pack Logix, testing is the backbone of our operations, ensuring that stringent quality control measures are applied to attain the best outcome for our customers. State-of-the-art technology and techniques such as FTIR, spectrophotometer, and Karl Fisher Titration ASTM D6304 method, are seamlessly integrated into every step. We diligently follow testing methods.
Our extensive quality control processes include frequent checks every five minutes for seal integrity, bottle cleanliness, date code accuracy, label application, and weight. Additionally, our dedicated quality inspectors conduct random checks throughout the day to ensure ongoing consistency.
There will never be more than five minutes that goes by without checking to make sure that the seal is good, the label is good, the inkjet is good, the fluid is the correct amount, and so on. We are diligent in our testing.
— MAIKEL CORREA, Quality Manager
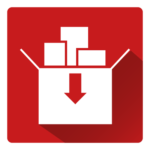
1
Incoming material inspection
We meticulously inspect all incoming materials to verify they meet our stringent quality standards. This process includes verifying the chemical composition, consistency, and purity of raw materials before they enter our production line.
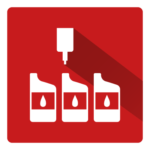
2
Precise Filling Operations
Our state-of-the-art filling equipment is calibrated to deliver precise amounts of product into each container. We use advanced technology to minimize variation and confirm consistency, maintaining the highest standards of accuracy and efficiency.
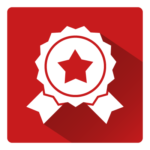
3
continuous QUALITY CHECKS
We conduct continuous in-process quality checks every five minutes. Our team monitors critical parameters such as weight, viscosity, and sealing integrity. Quantitative and visual inspection data are cataloged and available to our customers free of charge.
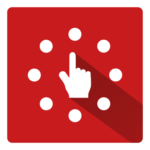
4
RANDOM
INSPECTIONS
Our dedicated quality technician conducts random checks on the line to validate that the highest standards are met. Randomly inspected shipments are marked with “Inspected Tape.”
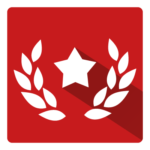
5
PRE-SHIPPING QUALITY TESTING
After filling, we conduct comprehensive testing on finished products, including leak tests, performance tests, and compatibility tests, to assure the product performs flawlessly under various conditions.
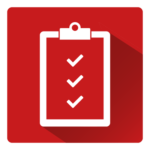